Do you need flux to solder?
The question of whether flux is required during soldering is a subject that frequently comes up. Do you need flux to solder? In light of the fact that flux can be quite difficult to deal with, some individuals could be pondering if skipping it altogether would result in a decent soldered bond.
Flux: What is it?
Flux would be a material used throughout soldering to speed up the procedure by ensuring that the surface of metallic components is connected and avoiding oxidation of such alloys while the soldering process takes place.
Before warming the metal components with a heating element, soldering flux is applied to their surfaces as a glue or fluid. The flux aids in deoxidizing the metal parts and removing any oxide deposits that would prevent the creation of a solid, dependable soldered junction.
Additionally, it aids in reducing the surface pressure of such molten material, which makes it easier for the solder to move and create a solid connection with both metal components.
What kinds of flux are there to choose from?
Flux comes in a variety of varieties, some of which are frequently used in soldering.
The flux of rosin
This kind of flux, manufactured from pine resin, is among the most frequently used while soldering electronic components. A strong, dependable connection is created when it is triggered by the soldering iron’s temperature.
Liquid-soluble flux
This particular flux is created by combining water with a chemical accelerator. Since it is simple to remove moisture once the soldering procedure is over, it is frequently used while soldering electronic parts.
No-clean flux
The formulation of this flux ensures that there will be no residue left behind once the soldering procedure is over. Due to the lack of cleanup requirements and the electrical residue, it doesn’t leave behind, which might affect the final result. It is frequently used for soldering electrical components.
The flux of acid
For welding copper pipes as well as other substantial metal components, this kind of flux uses hydrochloric acid. Due to its hard-to-clean-up nature and potential to harm delicate computer chips, it isn’t frequently used in electrical soldering.
Flux is made of alcohol
This particular flux is produced using a combination of alcohol as well as a chemical activation. Due to the ease with which it can be removed using alcohol following connecting electronic systems, it is frequently employed in this operation.
Do you need flux to solder?
The majority of the time, flux is necessary for successful soldering. Metal edges that are bonded with solder are cleaned with the aid of soldering flux, which also stops the oxidation of alloys.
Do you need flux to solder? The quick explanation is that flux is necessary for soldering. This is why.
rlc talk
What role does flux play in soldering?
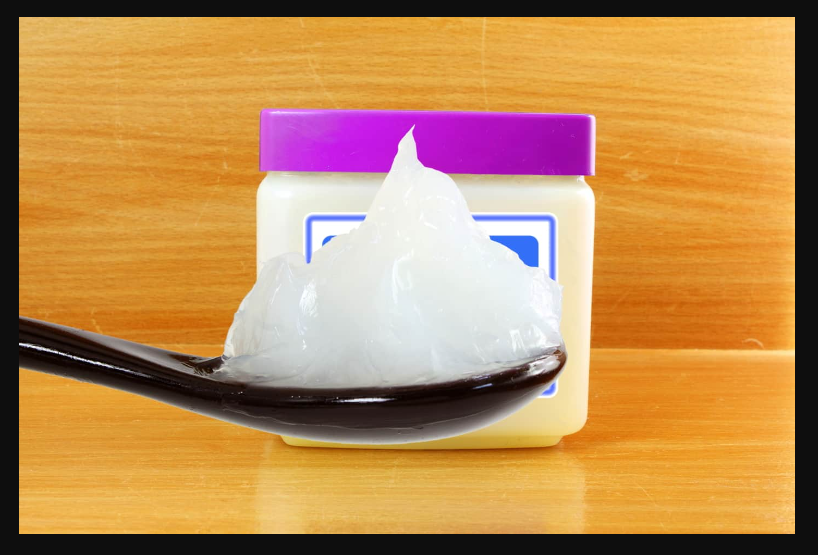
The construction of a solid, dependable soldered junction is made possible by flux, which is a vital part there in the soldering process. Gaining a stable soldered hub without flux could be challenging, and the union could be susceptible to failure.
Here are a few explanations for the question, “Do you need flux to solder?”
- Flux assists in cleaning the metal edges getting connected, eliminating any impurities or oxide coatings that might hinder the soldering procedure.
- Flux protects metal parts against oxidation, which might damage the soldered junction, during soldering.
- The melted solder may flow more smoothly and create a solid connection with both metal components because flux reduces its interfacial tension.
- Flux contributes to the prevention of metallic surfaces from re-oxidizing after the welding procedure is over, which can increase the dependability of the soldered junction over time.
You can see that flux is essential for the development of a solid, dependable soldered junction. Gaining a stable soldered hub without flux can be challenging, and the union could be vulnerable to failure.
Is it feasible to solder without the use of flux?
Despite the fact that it is technically feasible, it is typically only advised to solder with flux. Following are a few explanations on why soldering without flux is normally not recommended.
- It might be challenging to get a high-quality soldered junction when there are contaminants or oxide coatings on the metallic surface. Flux is a cleaning agent that aids in the removal of impurities and oxide layers from the metallic exterior, which is critical for a successful soldered procedure.
- The soldered junction may become weak if the metals oxidize while being soldered. Flux keeps the metal parts from oxidizing, resulting in a solid, dependable soldered hub.
- Without flux, this molten solder often has an excessively large surface tension, which could also create difficulties for the solder properly flow and solidify a connection with the metal components. Flux aids in lowering the interfacial pressure of the liquid solder, which makes it easier to flow and create a solid connection with the metal components.
In spite of the fact that it is theoretically feasible to solder without flux, it is normally advised to do so because of the aforementioned reasons. Although working with flux is a pain, the advantages it offers in terms of establishing a solid, dependable soldered bond make it very well worth the additional effort.
Therefore, the response to the question of whether flux is necessary for soldering is a loud “yes” that this next occasion you wonder about it.
What are some flux substitutes?
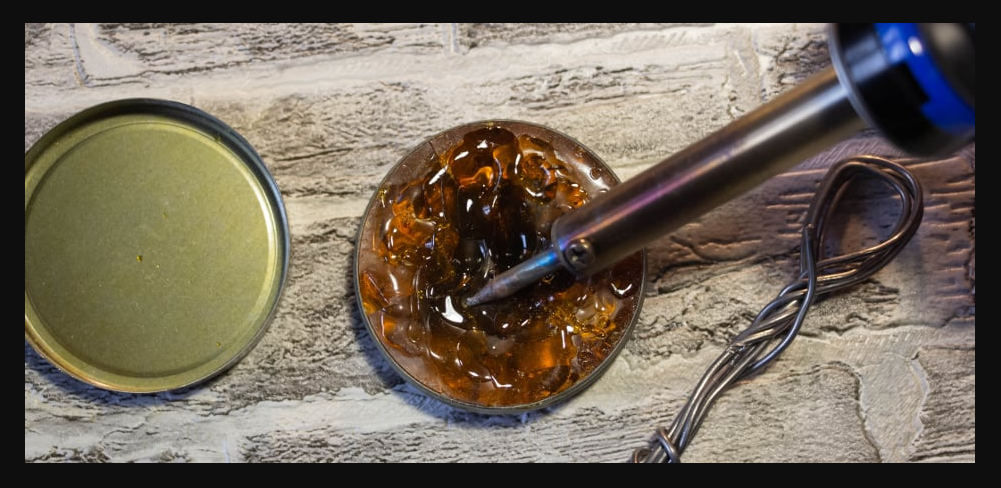
Flux performs a special function in enabling the construction of a solid, dependable soldered junction, making it impossible to substitute it during the soldering directly. Different soldering techniques exist, though, and they don’t involve the application of flux.
Laser Soldering
The employment of a laser-focused beam to burn and fuse the metal components is, however, one technique known as laser soldering. Since any impurities or oxide coatings on the metallic surface are vaporized by the extreme heat of laser light, laser soldering doesn’t need the application of flux. This efficiently cleans the metals and prevents oxidation throughout the soldering.
Soldering using ultrasound
Ultrasonic soldering is indeed an additional option that employs elevated vibrations to generate heat plus dissolve the metal components being connected. Since any impurities or oxide coatings on the metallic surface are vaporized by the extreme heat produced by the vibration, ultrasonic soldering, similar to laser soldering, doesn’t necessitate the application of flux.
Such unconventional soldering techniques can be helpful in some circumstances when the application of flux is impractical or where exceptionally clean different metals are necessary. They are frequently less popular than conventional soldering techniques that entail the use of flux.
Do I need Flux with Rosin Core Solder?
RLC talk
FAQs.
What sort of flux is used most frequently during soldering?
Soldering – a smaller version of welding?
Conclusion
Finally, flux is a crucial part of the soldering procedure. Therefore, please don’t overlook the flux the very next occasion you’re soldering since it’s an essential ingredient that will ensure that now every soldered link you create is sturdy and dependable.